COAL AND IRON
Extracting iron from iron ore
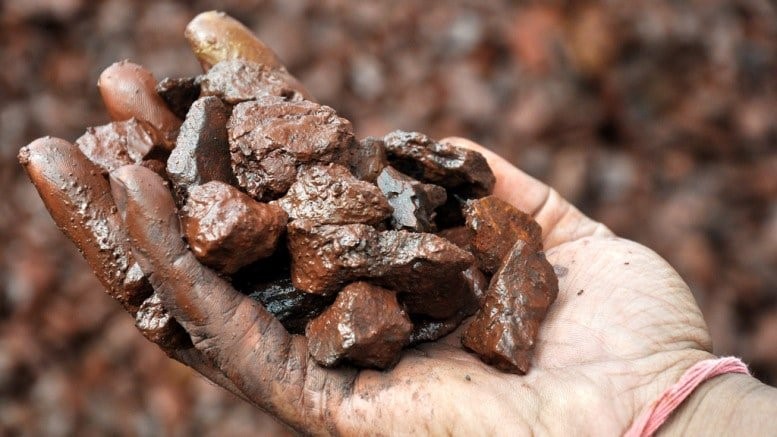
The process of manufacturing iron advanced with the extraction of iron from the ore. First, the ore was crushed into small pieces, which were then roasted to concentrate the iron content. Thereafter, the roasted ore went into the blast furnace for smelting. This involved introducing a heavy charge of charcoal, together with some limestone, through the top of the furnace and smelting it at a high temperature. Because the charge goes in at the top, and the smelted iron runs down into the bottom of the furnace, a high yield of iron is obtained, as hardly any of it ends up in the slag or waste, which floats in the form of a protective layer above the molten iron.
The molten iron was tapped and left to cool in moulds known as pigs. This pig iron was a brittle cast iron containing a high percentage of carbon (2-4%), which made it unsuitable for malleable or wrought iron. The pig iron therefore had to be re-smelted in special furnaces in the forge. This was know as the refining process, in which surplus carbon was burnt off, leaving the iron pure, soft and malleable or wrought.
På 1100-talet började man bryta järnmalm ur berget. Man lärde sig se hur det järnrika berget såg ut och kunde bryta loss bitar genom att sköra berget med eld. Det kallades tillmakning. Man arbetade sig från ytan och nedåt i berget och följde
Framställningsprocessen utvecklades med järnmalmsbrytningen. Först krossades järnmalmen till små bitar. Dessa rostades för att koncentrera järninnehållet. Den rostade järnmalmen smältes ned med mycket träkol och lite kalk i en masugn under.
Att tappa ut det smälta järnet kallades att "göra utslag". Det flytande järnet fick stelna i formar av sand till "tackor". Detta "tackjärn" var ett sprött gjutjärn med en hög kolhalt, ca 2-4% som ej dög till smide. Tackjärnet
Charcoal burning
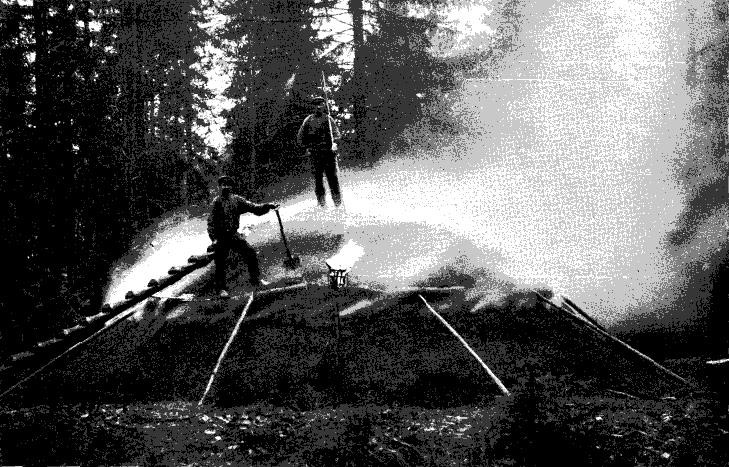
Building the stack and then covering it with broken coal and earth required equal measures of skill and care. Once the stack had been lit, the charring process would take two to three weeks.
There was always a danger that trapped gases would cause the stack to flare up suddenly, throwing off the broken coal and earth, with, at worst, the entire stack going up in flames. Voids could also occur, causing collapse of the stack, so the charcoal-burner had to sit watch over the stack continuously, day and night, and be ready to intervene at any time.
The charcoal produced from a stack would only be enough to keep the blast furnace fuelled for two days, yet it represented two or three weeks of work for the charcoal-burner. Still, it was absolutely vital that an adequate supply of charcoal was maintained. The stacks were usually sited as close to the smelting house as possible, one reason being that charcoal did not travel well and could easily crumble into unusable dust if shaken up too much during the journey.
De tidiga kolmilorna byggdes med veden liggande, men med vallonerna kom konsten att resa milorna som därmed blev effektivare. Att resa en mila och sedan täcka den med stybb och jord krävde kunnande och omsorg. Sedan milan tänts tog själva kolningen två till tre veckor.
Milan kunde "slå" vilket innebar att instängd gas blossade upp och stybbningen kastades av - risken var stor att milan brann upp. Mindre håligheter kunde uppstå inne i milan och förorsaka ras kolaren måste dygnet runt vaka över milan och vara beredd att ingripa.
Kolen från en mila räckte inte till mer än två dygn i masugnen, vilket alltså betydde ungefär två till tre veckors arbete I skogen. Att det fanns tillräckligt med kol var en nödvändighet. Kolet tålde heller inte att transporteras alltför långt, då det lätt kunde skaka sönder till oanvändbart stoft.
Blast furnaces
Blast furnaces in the Bergslagen region were first used sometime at the beginning of the 13th century, which was the period during which miners started to extract the iron from rock ore, instead of from bog or lake ore. The new blast furnaces soon replaced the old pit furnaces.
The blast furnace had a tall structure, with a central vertical shaft several metres in length and having a diameter at its widest point of 1-2 metres. The shaft was lined using a selected natural stone of clay mortar, reinforced with a further encircling wall of heavier stone and, finally, timber boxing. The area between the lining and the timber boxing was sealed using a fine-grained material-often sand and soil. Two vaults or passages, running in towards the centre, were created at the bottom: one, the tuyère, for blowing in air by means of water-driven bellows, and the other for tapping the molten iron and slag at regular intervals.
For practical reasons, blast furnaces were built alongside a fast-flowing watercourse, on which a water-wheel could be installed to drive the bellows. Ideally, the site would also be on the side of a hill, as the ore and charcoal could then readily be carted to the top of the furnace from the storage site on the level above. This type of blast furnace was built and in use up until the mid-19th century.
The remains of the ancient medieval smelting works are today no more than slag heaps and mounds. However, they could prove to be fruitful sites for archeological digs.
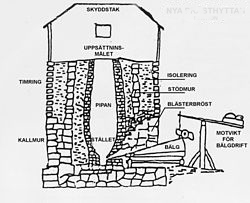
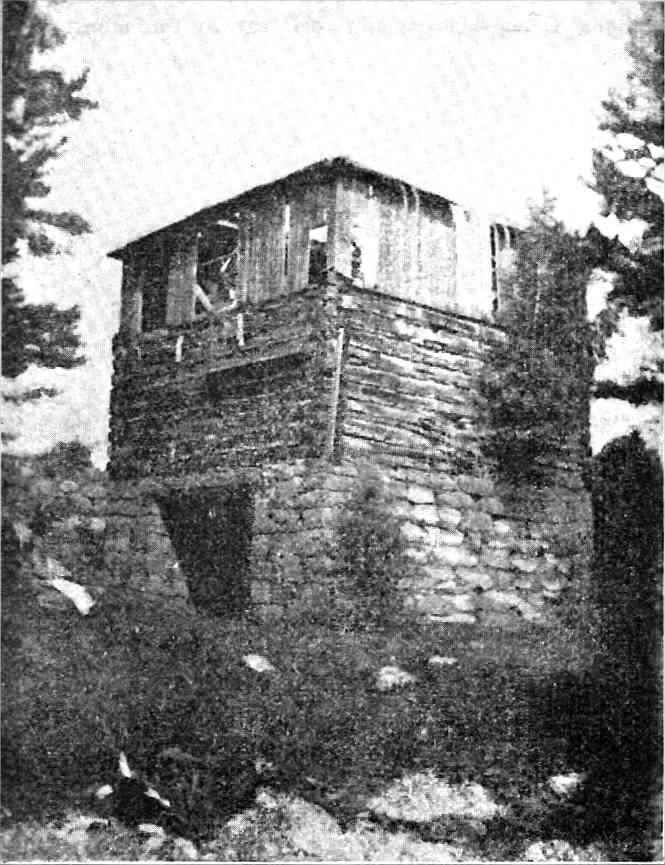
Rävåla blast furnace 1634-1865
Professional ironworkers, know as the Walloons (French-speaking Belgians), came to Sweden during the 17th century onwards, and introduced a new construction for blast furnaces, one without timber boxing. In the new design, the carefully sealed foundation wall of dressed stone continued all the way up, secured by iron ties. These were known as French-type or stone furnaces.
Various improvements, brought on by increasing competition, took place in blast-furnace engineering in the mid-19th century.
Gradually, the production of iron became increasingly concentrated, with fewer but larger blast furnaces located close to the new steelworks, with the charcoal fuel being replaced with coke produced from imported coal. Today, there are just two active blast furnaces in Sweden, one at Luleå and the other at Oxelösund.
A single day's output of iron at a modern steelworks is more than would have been produced in an entire year in a 17th-century smelting house!
Masugnen började användas i Bergslagen redan från omkring år 1200 i samband med att man övergick till att framställa järn ur bergmalm istället för myr- eller sjömalm. Masugnen kom mycket snabbt att ersätta den så kallade blästan. Det är en ugn byggd på höjden med ett schakt på flera meters djup och ursprungligen c:a 1-2 meters diameter på vidaste stället. Den murades med en innerpipa av utvald natursten i lerbruk, omgiven av en stödjande yttermurning en "bakmur" av grövre sten och längst ut en timmerkista. Tätande fyllning av finkornigt material, "mull" fanns mellan murningarna och ut mot kistan. Masugnen byggdes av praktiska skäl vid ett vattendrag med ett lämpligt fall, som kunde driva bälgarnas vattenhjul.
Dessutom skulle masugnen gärna stå i en backsluttning. Man kunde då bekvämt och praktiskt med kärra förra upp malm och kol till toppen av ugnen direkt från upplaget på planen ovanför.
En sådan masugn kallades mulltimmerhytta och byggdes och användes ända till 1800-talets mitt.Rester efter mycket gamla, övergivna hyttor från medeltiden består idag bara av en slagghög och en jordkulle. Det kan bli platser för arkeologiska undersökningar.
Yrkesfolk inom järnhanteringen kom till Sverige från Vallonien I Belgien under 1600-talet och framåt. De tillämpade ett nytt byggnadssätt för masugnar utan timmerkista.
Den noga hopfogade grundmuren av tuktad sten fortsattes hela vägen upp, sammanhållen av ankarjärn. Man talade om masugn av fransösk (fransk) typ eller stenmasugn.
Mot 1800-talets mitt infördes under trycket av ökande konkurrens olika förbättringar av masugnen, som gällde bränsleekonomi och produktions-volym. Steg för steg koncentrerades järnframställningen till allt färre och större masugnar, byggda i anslutning till nya stålverk och träkolet ersattes med koks, framställd ur importerade stenkol. I dag finns bara två masugnar i hela Sverige - en i Luleå och en i Oxelösund. Dagsproduktionen av järn överstiger årsproduktionen för en 1600-talshytta!
Homesteaders
The Swedish Bergsman or homesteader was an independent farmer and iron producer who owned his own land and forests. The ancient homesteader culture, which dates back to the Middle Ages, was a cooperative system for mining and smelting using blast furnaces.
Sometimes several villages would get together and build a smelting house. The homesteaders extracted iron from the iron ore, and supplied the pig iron to the ironworks, which would refine the pig iron into the all-important bar iron.A State mining authority ensured that the bar-iron forges were not sited too close to the smelting houses, blast furnaces and mines-with a view to protecting charcoal supplies.
The homesteaders would often not have the the technical skills required for making bar iron, and even their pig iron was of uneven quality. So they would often end up in conflict with the ironworks.
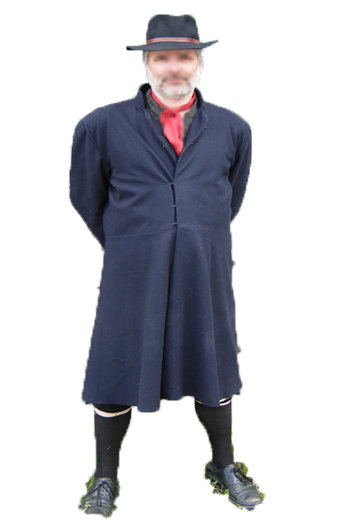
The homesteader villages consist of timber buildings, built little anyway, a reasonable distance from the jointly owned smelting house. Their work had to fit in with the demands of the farming year. Once the often meagre harvest had been gathered in at the end of the season, the homesteaders turned their attention to the forest and the mining of iron ore.
Many of the homesteadershad their own workers to do the hard work*. To light the fires they needed wood, but the really heavy consumption was generated by the demand from the blast furnace and, later, by the need for charcoal for the forge furnace*. The charcoal from one stack lasted no more than two days in the blast furnace. But it took 120 man-days to produce the charcoal and bring a load home. Generally, the production of pig iron would begin when the spring thaw started the rivers and streams flowing. The first job was to roast the ore in the pit furnaces until it was glowing. The blast furnace had to be fired and was fully charged with charcoal-it would take two weeks for the furnace to reach its operating temperature.
The ore was crushed into pieces the size of a cobnut or hazelnut, either on the ground or up near the top of the blast furnace where it would be stored in a special box. The stoker would introduce the charge, which would consist of a rotation of charcoal, limestone and iron ore, into the furnace, and it would then take about 15 hours for the charge to reach the bottom of the shaft. The number of days a homesteader would spend in the blast furnace would vary, but the stoker, who also tapped the melt, would know when the iron for the next homesteader had reached the hearth at the bottom.
Once the molten iron from the final charge of ore had been tapped at the bottom, leaving just the residual charcoal to burn itself out, the job was done. This was celebrated by partaking of some simple food, and by drinking "last-charge" beer , a ritual akin to a harvest festival. The pig iron would be carried into the store shed pending transport to the iron-weighing house and the ironworks.
The tight regulation that characterized mining and its associated activities is reminiscent of the way that livery companies or craft guilds operated. But as well as having been granted many rights, the homesteaders also had a duty-to produce iron. Nor were they allowed to sell their land to someone who merely wanted it for its forest.
* Våg Jan Persson and Våg Erik Jansson combined their farming with this kind of job
En bergsman var en självständig bonde och järnproducent med egen mark och egen skog. Den gamla bergsmanskulturen var ett kooperativt system för bergsbruk och masugnsdrift som inrättats redan under medeltid. Det kunde vara flera byar som gick samman och byggde en hytta. Det blev så att bergsmännen bröt järnmalm och drev masugnar och producerade tackjärn till bruken, som framställde det viktiga stångjärnet.
Statens kontrollorgan, Bergskollegium, övervakade att stångjärns-hamrarna inte byggdes för nära hyttor, masugnar och gruvor. Det var för kolförsörjningens skull. Bergsmännen saknade oftast den finansiella styrka och tekniska kompetens som krävdes för stångjärnsframställning. Även deras tackjärn hade ojämn kvalitet. De kom därför i konflikt med bruksägarna.
Bruksägarna försökte att säkra sin tackjärnsförsörjning genom att söka tillstånd för egna masugnar. Man lyckades ibland köpa in sig i kooperativa bergsmanshyttor genom att på det ena eller andra sättet förvärva bergsmanshemman. Man försökte även arrendera andelar i driften från overksamma bergsmän i hyttelagen. Bruksägarna bildade en klubb, Brukssocieteten, som i sin tur bildade en stark branschorganisation, instiftad med kungligt brev från 1747 och benämnd Jernkontoret. Jernkontoret tillhandahöll tekniska konsulter även för bergsmännens hyttdrift. Jernkontoret finns kvar än idag och ligger centralt i Stockholm.
Bergsmännens betydelse inom järnhanteringen avtog efterhand genom denna utveckling. Vissa driftiga individer ur deras krets gled så småningom in i en modernare roll som enskilda bruksägare, medan andra blev rätt och slätt bönder. De tvingande reglerna om bergsmännens verksamhet försvann i mitten av 1800-talet, men en del hyttelag fortsatte länge under oförändrade former.
Bergsmansbyarna består av timmerhus, uppresta litet hipp som happ, på något avstånd från den gemensamma hyttan. Bergsmannens arbete följde bondeårets rytm.
När han bärgat de oftast magra skördarna efter sommarens arbete med jordbruket var det dags att tänka på skogen och malmbrytningen. Malmen bröts genom tillmakning ända in på 1800-talet. Genom att elda mot berget blev det skört och kunde spettas loss.
Många bergsmän hade med sig egna drängar i det hårda arbetet. Tillmakningen krävde skog, men den stora virkeskonsumenten var masugnen och snart också smedjan med sina behov av träkol. Kolen från en mila räckte inte till mer än två dygn i masugnen - och det gick åt 120 dagsverken att kola och köra hem en mila.
Vid nyår kallade hyttfogden till hyttstämma. Då skulle varje bergsman - ofta var man inte mer än åtta i hyttelaget - ha kört sin malm till malmbacken och fyllt sitt kolhus med kol. Masmästaren som hade ansvar för blåsningen skulle ha murat upp "stället" - pipans nedre del - och sett över blåsbälgar, vattenhjul, rännor och dammar. Man kom överens om turordningen vid blåsningen och eftersom ugnen arbetade sämre mot slutet drog man ofta lott.
I allmänhet började tackjärnsproduktionen när vårfloden satte fart på bäcken. Malmen skulle nu först rostas i rostgroparna tills den blev glödande. Masugnen måste värmas upp och fylldes därför enbart med kol - först efter närmare två veckor har den fått upp tillräcklig temperatur.
Malmen krossades till hasselnötsstorlek nere på marken eller uppe vid masugnskransen och lades i ett särskildt bås. Kol och kalksten togs också upp. Masugnen packades av omväxlande kol, kalk och järnmalm av "uppsättaren". Det tog femton timmar för en uppsättning att gå ner genom pipan. Hur många dygn i masugnen en bergsman hade varierade, men masmästaren som skötte tappningen, "utslagen", visste när nästa bergsmans järn kom ner.
Det flytande järnet leddes till sandformar på marken och stelnade till tackjärn. Det fick både bergsmannens märke som hyttans nummer ingjutet.
Myndigheterna strävade efter att få bergsmännen att gå ihop och blanda sin malm gemensamt för att få fram jämnare kvaliteter, men förgäves!
De ville själva hålla kontroll över den egna malmen och den som hade dåligt rostad malm eller sur kol kunde straffas med att få blåsa sist. När sista uppsättningen var gjord, gick det så kallade drevet genom masugnen. Det firades med drevöl - en motsvarighet till skördefesterna. Man städade sedan upp kring hyttan och tog ut "klotet" det järn som blivit kvar i botten på ugnen. Slaggen hade lagts på de allt större slagghögarna om den inte gjutits till slaggsten för att användas som byggnadsmaterial. Tackjärnet bars in i järnbodarna i väntan på vidare transport till järnvågarna och bruken
När bergshanteringen dyker upp i de äldsta privilegiebreven tycks den redan relativt väl organiserad. Kanske hänger det samman med att den tar form under den stora lagstiftningens tid - den äldsta lagen, Västgötalagen, skrivs ned omkring 1220. Tidigt försökte staten av allt att döma hävda gruvorna som sin egendom. Gustav Vasa åberopar äldre handlingar när han skriver att "All malmberg i Sverige lyda till Sveriges krona".
Med privilegiebreven från 1300-talet gav man bergsmännen rätt att utnyttja gruvorna under bestämda villkor och dit hörde att betala en del av produktionen i skatt. Samtidigt slapp bergsmännen annan skatt och i privilegierna för Kopparberget och Åtvidaberg dyker för första gången ordet "bergsfrälse" upp. Områden med bergshantering fick sin egen lagstiftning som delvis starkt skiljde sig från landskapslagarna, dit hörde "täktekarlsrätten" - man hade rätt att fritt röja, odla och bygga på mark i närheten av gruvan och sedan lämna den i arv.
Hela bergshanteringen har med sin noggranna reglering många drag som påminner om skråväsendet. Bergsmannen hade inte bara rätt utan också skyldighet att framställa järn och han kunde inte sälja sin mark till någon som bara vill utnyttja skogen.
Continue to the next side/Gå vidare till nästa sida: